COLLABORATIONS
Industrial and Academic Collaborations
As a pioneer and market leader in conformal coatings technologies, Specialty Coating Systems has been a key innovator in the coatings industry, developing products and technologies such as ParyFree®, Parylene HT®, Parylene C-UVF® and the AdPro family of adhesion technologies. To further develop coating technologies and expand the use of coatings on advanced applications, SCS has collaborated with key industrial and academic partners on several projects over the past five decades.
SCS’ Switzerland facility, Comelec, has had a longstanding strategic partnership with Swiss Federal Institute of Technology Lausanne (EPFL). This collaboration has enabled the advanced hybrid deposition of multilayer coatings, including ALD+Parylene coatings. Comelec and EPFL continue to partner on ongoing projects, focusing on improving the technology for long-term active implantable medical devices (AIMDs).
SEALANT
2020 R11; 2024
The objective of the SEALANT project is to make soft encapsulation technologies safely applicable for AIMDs and eliminate the use of conventional bulky cans made of metal or glass for specific applications. The technology’s performance is to be investigated on different types of implants, ranging from adapting existing products to new breakthrough micro-optical implants for optogenetics.
This project utilizes multilayer coating technology, stacking multiple layers of Parylene and inorganic materials to provide advanced barrier properties. While conventional Parylene is an essential coating in the medical device industry, multilayer coatings have not been widely explored for use in AIMDs. The SEALANT project uses this advanced coating technology to create new encapsulation methods that can be applied to a broader range of products, enabling the development of new implantable products.
RELIEVE
2018 R11; 2021
RELIEVE sought to provide a bioelectronic solution to relieve patients from chronic headaches through neuromodulation without the severe side effects that are commonly experienced with pharmaceuticals. The extremely miniaturized and flexible RELIEVE bioelectronic implantable system conformed to the patient’s anatomy, allowing it to be implanted during a short outpatient procedure. This was made possible by replacing conventional bulk implant housings (metal, glass or ceramic cans) with an innovative soft encapsulation approach through the use of advanced multilayer coating technologies.
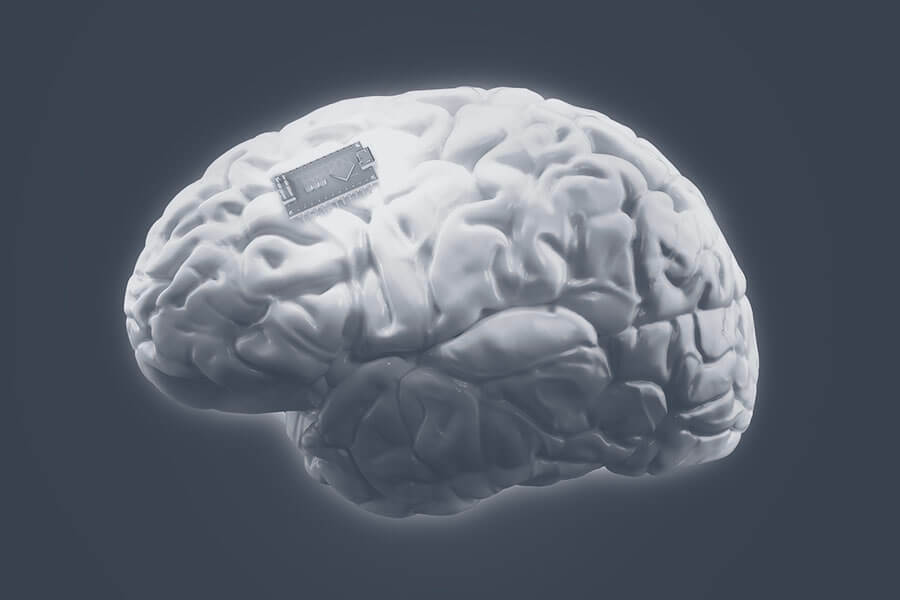
POSITION
2018 R11; 2021
This goal of POSITION was to enable innovation in smart catheters and implants with the introduction of open technology platforms for miniaturization, in-tip AD conversion, wireless communication, MEMS transducer technology and encapsulation. These platforms are open to multiple users and for multiple applications. Multilayer coatings technologies were used to address encapsulation challenges, enabling the next AIMD generation. Learn more about POSITION.
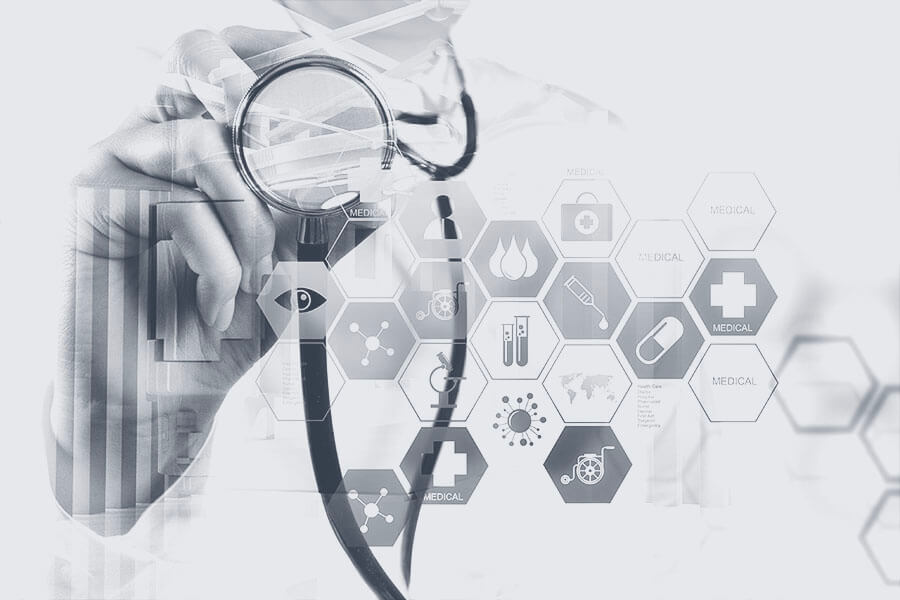
XInoCaps
2017 R11; 2020
Through a collaboration with EPFL, XInoCaps developed Parylene/inorganic multilayer coatings with advanced barrier properties. These coatings combine Parylene C and inorganic thin films (from an ALD and / or PECVD process). This project allowed for the improvement of hybrid multilayer coating equipment platforms. Specifically, the EPFL Laboratory for Processing of Advanced Composites (LPAC) characterized and modeled the multilayer structures to improve both mechanical behavior and barrier performances. The EPFL Laboratory for Soft BioElectronic Interface (LSBI) integrated and evaluated performances of these innovative coatings in electrically active devices towards the development of flexible implants; the EPFL Swiss Plasma Center (SPC) focused on plasma sources design.
The ultimate goal was to define multilayer stacks and procedures to encapsulate any device at low temperature and trigger the development of new miniaturized and flexible biomedical implants with improved lifetime and reliability.
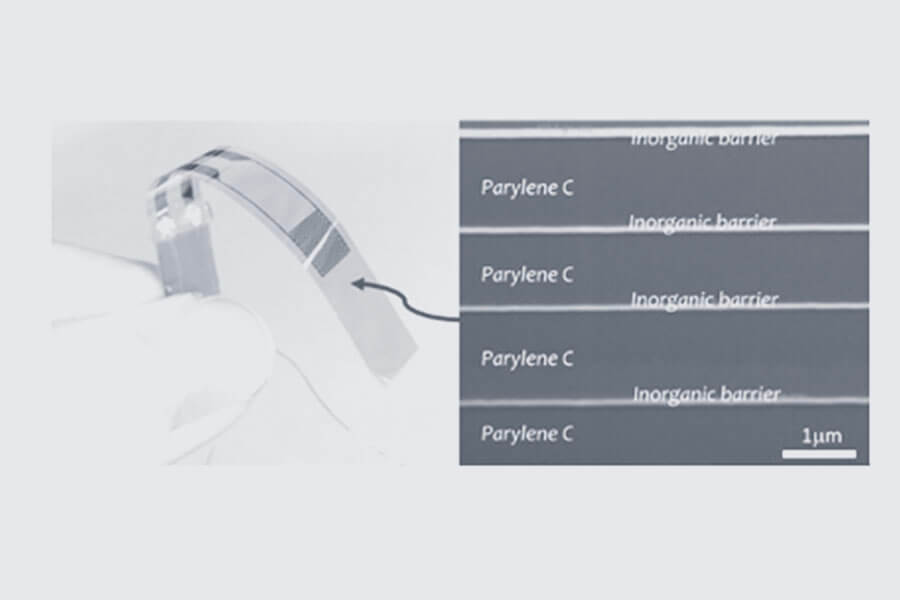
InForMed
2015 R11; 2028
The purpose of InForMed was to establish an integrated pilot line for medical devices. The pilot line included micro-fabrication, assembly and encapsulation. The core of this chain was the micro-fabrication and assembly facility of Philips Innovation Services.
Providing an industrial micro-fabrication and assembly facility where new materials could be processed and assembled enabled emerging markets – especially in smart, minimally invasive instruments and point-of-care diagnostic equipment – and stimulated the development of entirely new markets. The pilot line was integrated in a complete innovation value chain from technology concept to high-volume production and system qualification. Protocols were developed to ensure an efficient technology transfer between the different links in the value chain. Parylene technology was part of this pilot line, providing the final biocompatible encapsulation solution.
