ALD COATINGS OVERVIEW
ALD Coatings
Atomic layer deposition (ALD) is a type of chemical vapor deposition that creates thin-film Al2O3, TiO2, SiO2 or HfO2 coatings by introducing a gaseous reactant, or precursor, into the reaction chamber to trigger a chemical surface reaction on the substrate. The resulting ALD coatings are grown, layer by layer, directly onto three dimensional substrates in a perfect, conformal coating to ensure optimal protection against oxidation, moisture or degradation.
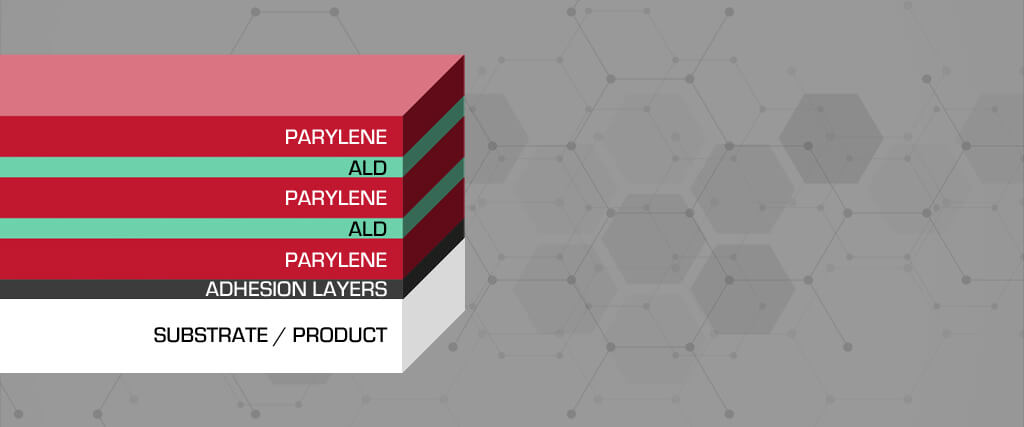
ALD+Parylene Multilayer Coatings
ALD+Parylene combines atomic layer deposition coatings with Parylene polymer coatings to form an enhanced multilayer coating that offers increased barrier properties to protect devices in extreme environments. Combining the protection of organic Parylene with inorganic ALD coatings (i.e., Al2O3, TiO2, SiO2, HfO2) creates a robust protective solution in an ultra-thin coating. ALD+Parylene offers 3D conformity for complex and miniature components and provides improved barrier protection against water, vapor and gases at ultra-thin levels. Additionally, the multilayer coating has outstanding mechanical properties and excellent biostability.
ALD+Parylene multilayer technology is generated through a unique hybrid deposition process. Multiple layers of ALD and Parylene coatings are applied in a way that leads to very controlled layer growth, resulting in total thicknesses ranging from 1- 10 microns.
Properties of ALD+Parylene Coatings
- Ultra-thin, uniform films (generally 1-10 microns)
- Superior protection against oxidation and moisture
- Biocompatibility
- Excellent thermal stability
- 3D conformity
Benefits of SCS
- Worldwide production capabilities for manufacturers and suppliers
- AS/EN 9100 and ISO 9001 certified coating centers
- Production Parts Approval Process (PPAP)
- Meets the requirements of IPC-CC-830
- Over 50 years of conformal coatings experience
Reworking ALD Coatings
ALD coatings are resistant to chemicals and solvents, which makes them difficult to rework. If reworking is necessary, mechanical means to remove the coating, such as abrasive materials or an excimer laser may be the best option. Once the coating is removed and any updates, upgrades or repairs are completed on the technology, the coating can be reapplied.
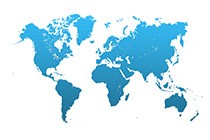
A global network of coating centers ready for your application.
Specialty Coating Systems offers customers regionally-located coating facilities to handle their engineering and production requirements. To discuss the benefits and properties of conformal coatings and your protection needs with an applications specialist, contact us online or call +1.317.244.1200.