LIQUID COATINGS OVERVIEW
Liquid Coatings
Liquid conformal coatings form an encapsulating layer to protect devices and components from contamination, moisture damage, temperature extremes and corrosion. Wet processes are used to apply liquid coatings and include brushing coating material onto the substrate surface, dipping the substrate into coating, and spraying the coating material onto the substrate – either by manual or automated methods.
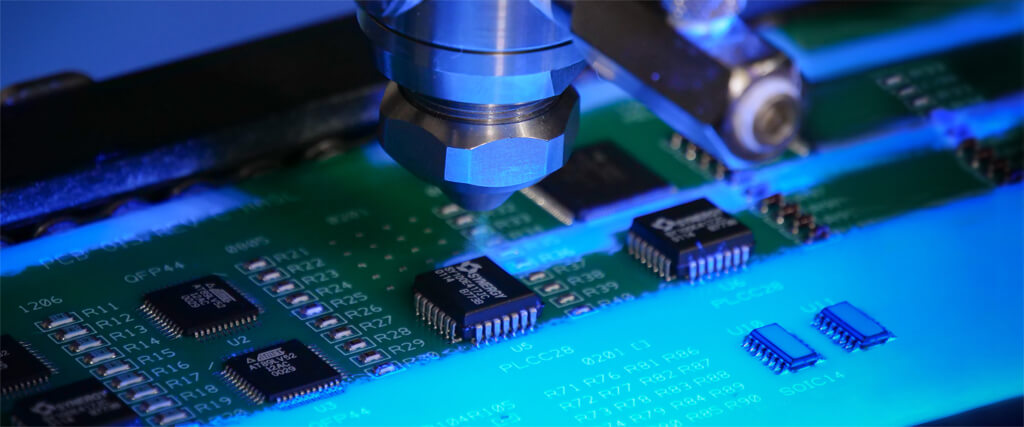
There are several types of liquid coatings, including acrylic resins (AR), epoxy resins (ER), silicones, polyurethanes and styrene rubber co-polymers to name a few. Each coating type offers its own unique properties and characteristics, including dielectric strength, moisture barrier, high heat resistance, ability to be reworked, etc. Within each coating family, there are also numerous variants that offer differentiating properties to uniquely meet the needs of specific applications.
Types of Liquid Coatings
- Acrylic coatings offer excellent moisture and humidity resistance can also prevent the growth of fungus.
- Epoxy coatings offer extreme hardness, providing exceptional coating strength and abrasion resistance as well as excellent chemical and temperature resistance.
- Silicone coatings are incredibly versatile with excellent adhesion and resistance to heat, moisture and UV light.
- Polyurethane coatings offer resistance to chemicals, minimal moisture penetration and are excellent dielectric barriers.
Industries
- Consumer electronics
- Medical
- Electronics
- Aerospace
- Defense
- Automotive
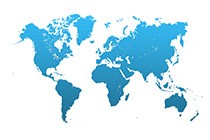
Connect with Our Global Network of Liquid Conformal Coating Centers
Specialty Coating Systems offers customers regionally-located coating facilities to handle their engineering and production requirements. To discuss the benefits and properties of liquid coatings with an applications specialist, contact us online or call +1.317.244.1200.